From natural gas to hydrogen in a matter of days
March 11, 2024
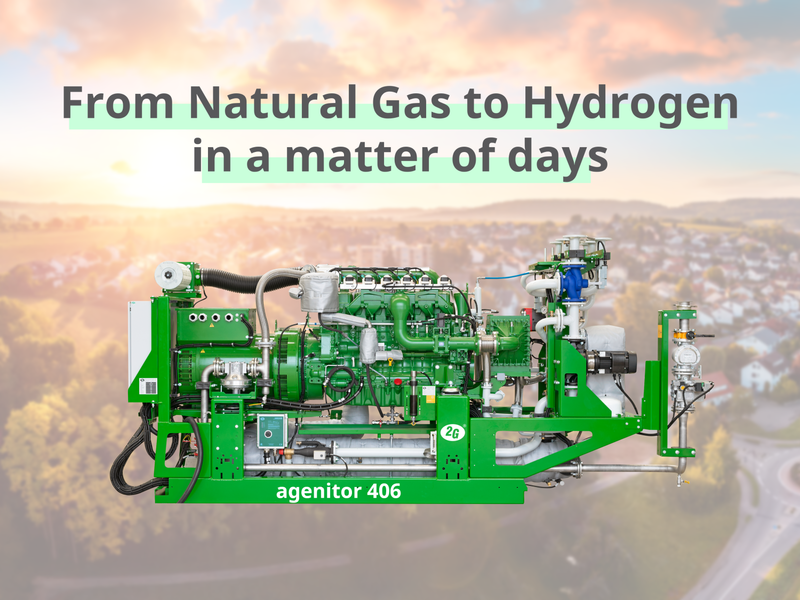
German premier in Eastern Bavarian town Amberg: a natural gas CHP was converted to run purely on hydrogen. The system is being used for research.
The Center of Excellence for Cogeneration Technologies (CeCoGen) at the Technical University of Applied Sciences Amberg-Weiden in Eastern Bavaria cooperated with the CHP manufacturer 2G Energy from Heek for the first retrofitting of a natural gas combined heat and power system to run on hydrogen in Germany. The system began running on the new fuel last October. The system was complemented by a hydrogen supply system with a central storage. The CHP is part of the Cogeneration technology center on the campus of the Technical University of Applied Sciences Amberg-Weiden and is used for research to gain further insight on how to make the hydrogen operation more efficient and even safer. The researchers regularly publish their findings.
A natural gas CHP of the 2G model agenitor 406 with an electrical output of 250 kW and a thermal output of 260 kW was the object of this retrofitting. The original system was installed in March 2019 and has since been used to take measurements for various research activities.
In an interview with E&M, Max Becker explained that the retrofitting did not cause any major problems. As project lead at the Institute for Energy Technology (Institut für Energietechnik, IfE GmbH), he managed the project on behalf of the Technical University. He states: "It was by no means a standard procedure, even for the technicians. But we didn't encounter any problems and within a couple of days, the hardware was replaced." Apparently, adjustments to the control system were more of a challenge. Additionally, the converted 6-cylinder engine can not yet produce the original output compared to when it ran on natural gas – but the research is focused on changing that.
The CHP and heat pump manufacturer 2G Energy has been working with the Technical University Amberg-Weiden for some years now. The installation of the hydrogen CHP for the municipal utility of Haßfurt in 2019 was already a product of this cooperation. "This pilot unit was also used to perform extensive measurements," explains Becker. However, that was always a logistical challenge for the Technical University. With a hydrogen CHP on the premises, basically on the own doorstep, the researchers' job has become far easier. The Free State of Bavaria financed the retrofitting of the research unit in Amberg-Weiden via the basic financing given to the CeCoGen. According to the manufacturer, the modularized approach 2G Energy has been taking to system design for several years already, contributed to the prevention of major problems with the technical implementation. The modular design ensured that only a few components needed to be replaced to make running on hydrogen possible.
The technical retrofitting measures were focused on the changed pressure ratios in the form of different pistons being used and the adjustment of the mixture composition process to the new fuel. "The compression had to be reduced to suit hydrogen as a fuel," says Becker. When natural gas or biogas are being used as fuel, the mixture is composed inside the gas mixer before being compressed inside the turbocharger. When hydrogen serves as fuel, however, the mixture forms directly in front of the combustion chamber when the hydrogen is injected into the intake manifold.
All of this is due to the characteristics of hydrogen: Hydrogen is much more flammable than natural gas while also having a higher laminar flame speed, meaning that hydrogen is much more susceptible to cause flashbacks inside the intake manifold.
Hardware conversion within limits of traditional engine technology
The standardization of pistons and gas injectors in systems by 2G Energy has progressed so far that they can be retrofitted without a problem, as proven in Amberg. At worst, technicians might not yet be familiar with handling six individual gas injectors instead of a single gas mixer. "That's the most significant difference to natural gas systems and might be seen as a challenge by some," adds Frank Grewe, CTO of 2G Energy. "Once everybody gets used to it, it will become routine business."
The turbocharger of the CHP was also replaced to allow for an increased air-fuel ratio in hydrogen operation. Furthermore, the system required a control system and software update, among other things, to adjust the ignition timings, ramp-up settings and control strategies to the new fuel.
According to 2G Energy, the CHP is approved for an output of 170 kW in hydrogen operation and 250 kW in natural-gas operation. "Due to the fuel characteristics of hydrogen, the pistons don't compress as much, leading to a reduced output," explains Max Becker. He reiterates that researching the operation with higher outputs is critical to increase efficiency going forward: "The research unit helps us to push the limits." Currently, the CHP operation is only safe up to 170 kW. Becker explains that, beyond that point, there would be a risk of spontaneous ignitions that could damage the engine in the long run. Therefore, homogenizing the mixture is another key factor for the researchers. To find a way to optimize the air-hydrogen mixture, the system has been equipped with optical measuring systems. They allow researchers to observe the combustion from within the system, which - they hope - can provide valuable insights. Grewe elaborates: "The system being installed on the premises of a university, it only makes sense for us, as well as the Technical University Amberg-Weiden and its students, to take a deeper look into the system. The optical measuring technology built into this system is not part of the standard sensors. It allows researchers to observe the combustion chamber. Two combustion chamber sensors with twelve light cones each allow them to see even the fringes of the combustion chamber."
According to Grewe, hydrogen engines by 2G Energy have a mean pressure of up to 14 bar while natural gas engines can reach up to 18 bar. "On our development test bench in Heek, we operate hydrogen systems with the same 18 bar, so the overall performance is identical. The researchers in Amberg are authorized to do the same for the scientific research into the operation with higher outputs," says Grewe.
Research in cooperation with multiple partners
The retrofitted CHP is part of a larger research network. Alongside eight other partners, the Technical University Amberg-Weiden and 2G Energy contribute to a research project on technological solutions for high-efficiency zero-emission hydrogen engines in cogeneration applications (CH2P). The project strives to increase the units' power density as a means to increase efficiency and reduce costs.
As far as the Technical University Amberg-Weiden is concerned, the retrofitting was only the first step. Further research activities are intended to complement the growing hydrogen economy on a scientific level. "With our research system, we will now try to lower cost level even further and bring the emissions as close to zero as possible. To this end, we observe all the critical system components and optimize them in detail using the most recent experimental methods and simulation tools," is how Professor Raphael Lechner of CeCoGen explained the project when Bavaria's minister of economy, Hubert Aiwanger, visited the system last October. With regard to the future, Lechner explains that the CHP is supposed to have multiple supports: "We want a combined solution, so a system that can run on natural gas, biogas or biomethane mixed with any share of hydrogen.”
Key components of the retrofitting
- Turbocharging system with exhaust wastegate
- Pistons
- Gas train suited to hydrogen incl. safety devices
- Gas rail with hydrogen injectors
- Injector control unit
- Safety devices (such as gas detection sensors, automatic shut-off valve)
- Software adjustments
The system at a glance:
Operator:Tech. Univ. of Applied Sciences Amberg-Weiden System: Existing system converted from natural gas to hydrogen, type 2G agenitor 406 with an electrical output of 250 kW and a thermal output of 260 kW, current hydrogen operation at 170 kW electrical output.
Particularity: Existing system used in research retrofitted to run on up to 100% hydrogen