Fournisseur décentralisé
Privatmolkerei Naarmann et 2G réalisent un projet de suivi avec 1 MWel
Faits et chiffres
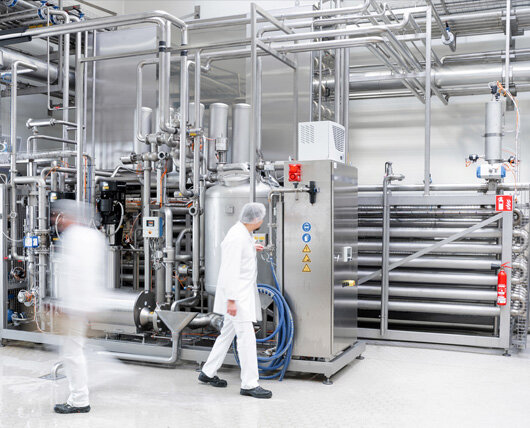
Chaleur, refroidissement et électricité - la transformation des produits laitiers nécessite constamment de grandes quantités d'énergie. Cela est dû à des processus comme la pasteurisation, la réfrigération du lait cru et des produits laitiers, le fonctionnement des séparateurs ou des machines d'homogénéisation qui se produisent 24 heures sur 24 dans la plupart des entreprises de transformation laitière. L'usine de la Privatmolkerei Naarmann GmbH située à Neuenkirchen est également active tous les sept jours de la semaine et transforme environ 200 000 tonnes de lait cru par an en lait UHT, crème, sauces, puddings, concentrés, poudres et de nombreux autres produits qui sont principalement destinés aux gros consommateurs, au secteur de la restauration, à l'industrie alimentaire ou destinés à l'exportation.
La cogénération couvre la demande constante de chaleur et d'électricité
La demande simultanée et constante d'énergie électrique et thermique tout au long de l'année crée des conditions optimales pour l'utilisation des systèmes de production combinée de chaleur et d'électricité (CHP). C'est pourquoi Naarmann mise depuis longtemps sur une cogénération au gaz naturel par 2G : Un patruus 400 est utilisé sur le site de l'entreprise depuis 2014. Installé dans un conteneur highline insonorisé, il fournit à l'usine une production de jusqu'à 400 kWel et 504 kW thermique. La chaleur est acheminée vers les consommateurs ou temporairement stockée dans un ballon tampon d'une capacité de 100 m³ – pour extraire la chaleur lors des pics de charge – à des températures de départ et de retour de 95 °C et 75 °C respectivement.
"L'exploitation de notre propre système de cogénération au lieu d'acheter séparément de l'électricité et de la chaleur auprès de fournisseurs externes augmente non seulement notre efficacité économique, mais réduit également les émissions de CO2 dans l'ensemble", explique Matthias Kemper, responsable des systèmes énergétiques chez Naarmann. Cependant, il rapporte également que la demande d'énergie a augmenté avec l'expansion des capacités de production au cours des dernières années. "C'est pourquoi nous avons voulu exploiter d'autres opportunités pour augmenter l'efficacité."
Efficacité accrue en combinant la cogénération avec un générateur de vapeur
En 2018, Naarmann a voulu affiner le principe éprouvé de la production combinée de chaleur et d'électricité : les nouveaux systèmes devaient fournir de l'électricité et des niveaux élevés de chaleur ainsi que de la réfrigération. À cette fin, Kemper souhaitait combiner la technologie de cogénération avec une machine frigorifique à absorption ainsi que la génération de vapeur chaude pour le traitement à ultra-haute température. En parallèle, la direction souhaitait une solution avec un rendement électrique élevé car l'électricité produite par cogénération sur site est beaucoup moins chère que de l'acheter à un fournisseur.
Les exigences élevées en matière d'efficacité ont été déterminantes dans la décision de laisser à nouveau 2G fournir la cogénération. "Ce n'est pas seulement l'efficacité qui frappe le sweet spot - les systèmes nous ont également convaincus avec leur énorme puissance électrique", explique Kemper, qui a pris en charge le projet, la décision. "Évidemment, il y avait aussi des facteurs soft comme un bon SAV en faveur de la 2G", ajoute le responsable énergie qui se souvient : "L'équipe d'ingénierie de la 2G reste disponible même après la mise en service et avec l'ancienne cogénération, par exemple. , cela nous a permis d'optimiser l'extraction de chaleur même après une mise en service réussie.“
Les nouveaux systèmes combinés de chaleur et d'électricité offrent une puissance électrique d'un mégawatt
Cette fois, les planificateurs ont choisi les modèles CHP agnitor 408“ et avus 500plus qui ont ensuite été installés dans des conteneurs insonorisés également – ils fonctionnent sans problème depuis environ un an maintenant. L'isolation acoustique réduit les niveaux de bruit pendant le fonctionnement à environ 45 dB(A) à dix mètres, ce qui était particulièrement important pour Naarmann, en raison de la proximité de l'installation avec les bâtiments résidentiels voisins. L'agenitor 408 fournit environ 360 kWel et convertit environ 42,5% de l'énergie primaire contenue dans le combustible en électricité. Il produit également jusqu'à 381 kW d'énergie thermique. Le deuxième nouveau CHP, un avus 500plus, a une efficacité électrique similaire, mais offre encore plus de puissance – dans ce cas jusqu'à 550 kWel et 578 kW thermiques.
La chaleur générée par les deux moteurs est extraite à des températures proches de 84 °C et mise à disposition de la machine frigorifique à absorption, tandis que la chaleur extraite du système d'échappement peut monter jusqu'à 420 °C et est mise à disposition du générateur de vapeur dans un circuit séparé, troisième conteneur insonorisé.
La technologie de réfrigération permet de réaliser des économies
A l'intérieur d'un réservoir de retour, les puissances frigorifiques fournies par la machine frigorifique à absorption sont utilisées pour amorcer le refroidissement du réfrigérant, ici de l'eau glacée. Cela soulage la pression sur la technologie de réfrigération conventionnelle. "Cela permet d'économiser tellement d'énergie que cela soulage notre système de réfrigération, qui est également nouveau", explique le responsable de l'énergie.
Contrairement au patruus CHP, les deux nouveaux systèmes sont orientés vers la production d'électricité. L'objectif : minimiser la quantité d'électricité achetée auprès de fournisseurs externes. C'était l'un des arguments en faveur de l'acquisition de deux centrales de cogénération d'une puissance électrique combinée d'environ un mégawatt. Désormais, les capacités de production d'électricité sont si importantes que des achats d'électricité notables ne sont nécessaires que lors des pics de consommation ou lorsque la cogénération est en service. Un autre avantage de l'autosuffisance est que les fournisseurs et les gestionnaires de réseau doivent réserver moins de capacité, ce qui a un effet positif sur les charges. Combiné avec un système planifié de gestion de la charge de pointe qui utilise le système de stockage de glace nouvellement installé comme tampon et évite ainsi les pics de consommation d'électricité par la technologie de réfrigération, beaucoup d'argent peut être économisé.
Le mode de contrôle sans injection réduit la facture du fournisseur
Dans un esprit d'efficacité maximale, les nouvelles CHP fonctionnent pratiquement sans pause mais pas toujours à pleine charge. La quantité d'énergie mise à disposition est dictée par la commande d'alimentation nulle. Il régule les deux machines pour qu'elles suivent au plus près la courbe de demande d'électricité. Cette méthode de contrôle assure également une répartition égale de la charge. Cela signifie que les heures de fonctionnement et l'usure sont réparties uniformément entre les unités de puissance. Grâce à une fonction d'accès à distance des utilisateurs autorisés via Internet intégrée au système de contrôle, l'état des groupes électrogènes peut être surveillé à distance par l'opérateur, un gestionnaire d'énergie dans ce cas, et les techniciens de 2G.
L'autoproduction couvre 92% des besoins en électricité
Un an s'est écoulé depuis la mise en service des deux nouveaux systèmes de production combinée de chaleur et d'électricité et le concept de Kemper a déjà été validé. Le mode de régulation à injection nulle fonctionne avec une extrême précision : 97,6 % des capacités d'énergie autoproduite sont utilisées - malgré des travaux de maintenance occasionnels. De plus, le degré d'autosuffisance a augmenté massivement. Grâce aux nouveaux systèmes financés par des subventions du Fonds européen agricole pour le développement rural, Naarmann peut désormais couvrir 92 % de ses propres besoins en électricité. "Et c'est aussi bon pour l'environnement", dit Kemper. "Grâce à la nouvelle cogénération, à l'intégration du générateur de vapeur dans la ligne de la chaleur extraite et au système de réfrigération plus efficace, environ 3 600 tonnes d'émissions de CO2 sont évitées chaque année."







